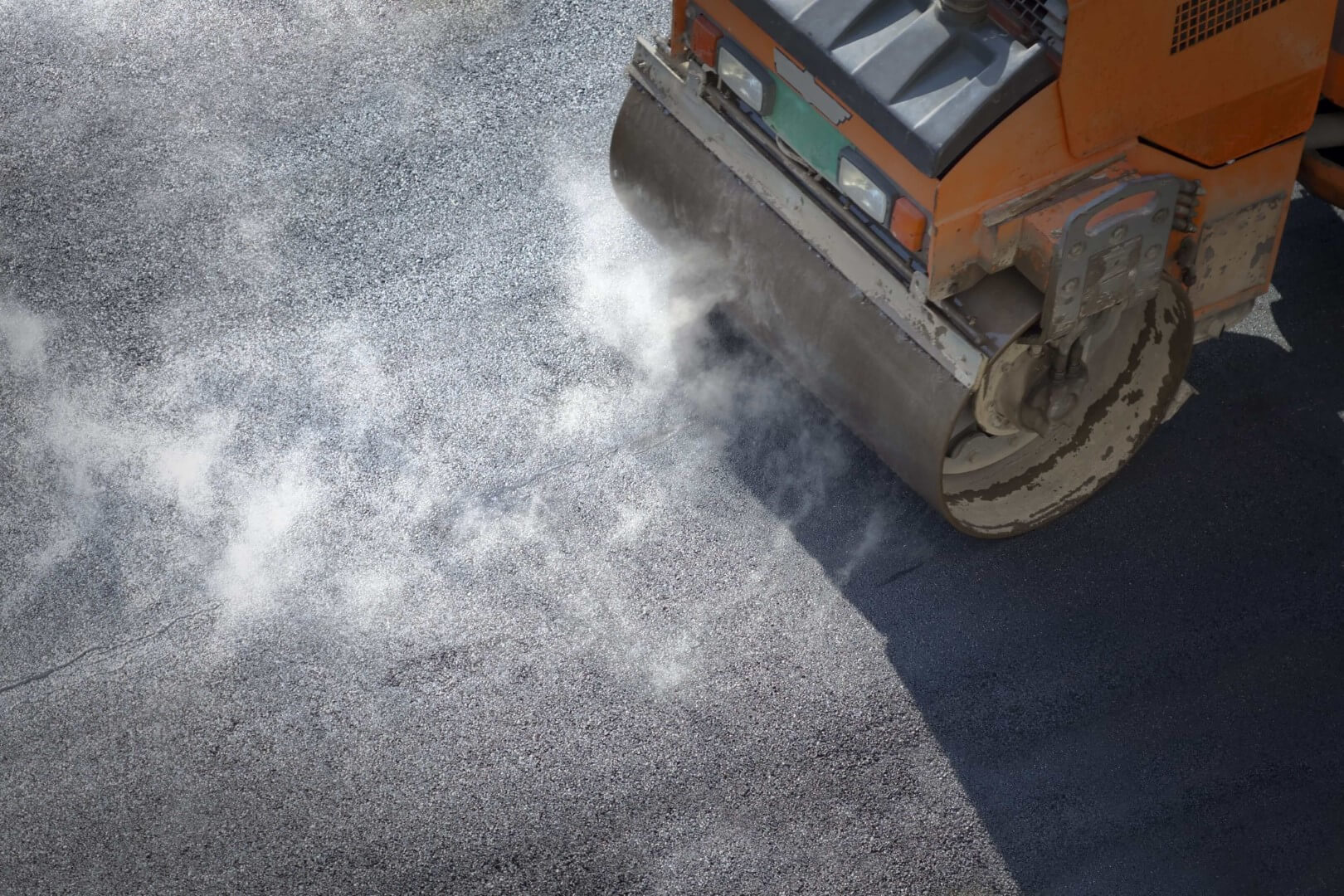
Sustainable Polymers for Asphalt
With roads in over 30 countries across the world, MacRebur are the leaders in offering asphalt producers both financial and environmental savings through the use of our innovative products.
View ProductsWhy MacRebur?
Savings
Using our MR6 and MR8 products, asphalt plants can save significantly on their production of standard and modified asphalt mixes.
Quality
Consistency of product is vital for all of our operations. We form partnerships only with those who can supply us with the most consistent materials.
Knowledge
We work with highly regarded academics across the globe and have access to, and commission, research at the forefront of the field.
Experience
Currently active in 30+ countries across the world, we are known for producing the best sustainable polymers on the market.
Products
All of our carbon data is verified in accordance with ISO 14064-3.
MR6
MR6 is manufactured from a mix of polymers and is designed to modify asphalt and reduce deformation failures or increase stiffness.
Typically dry mixed at asphalt plant, MR6 is used where traditionally polymer modified bitumen's (PMBs) are specified. This might be on motorways, heavy duty base courses or where surface courses are subject to heavily loaded traffic.
MR6 provides a direct replacement to virgin polymer, used in the production of PMB.
On average MR6 saves 11.32 kgC02e per tonne of asphalt
MR6
MR8
MR8 is manufactured from a mix of polymers and is designed to extend the binder in any asphalt mix.
The product is used where unmodified binder (liquid asphalt) is normally specified, for instance all base, binder and surface course asphalt material on standard traffic roads, footways, etc.
MR8 is used as a direct replacement for neat binder used in asphalt and is typically dry mixed at asphalt plant.
On average MR8 saves 4.65 kgC02e per tonne of asphalt
MR8
Sustainability
Safe for use
Our products are rigorously tested to ensure they are safe for both humans and the environment.
ISO accredited
We provide real world accredited carbon savings. All carbon data noted is verified in accordance with ISO 14064-3.
Sustainable technologies
By extending part of the Bitumen in the mix, our products reduce fossil fuel usage, leading to a reduction in carbon footprint.
Projects
Barcelona, Spain
View ProjectEnfield, UK
View ProjectSelangor, Malaysia
View ProjectPaldiski, Estonia
View ProjectZermatt, Switzerland
View ProjectSainsbury's Barnwood Resurfacing Project
View ProjectBusaiteen Development - Bahrain
View ProjectNew York City DOT - Staten Island
View ProjectAuckland International Airport - New Zealand
View ProjectRogaland Region of Western Norway
View ProjectVirginia DOT MR6 - USA
View ProjectNew Jersey Turnpike - USA
View ProjectBarcelona City Bus Lanes
View ProjectMeet the team
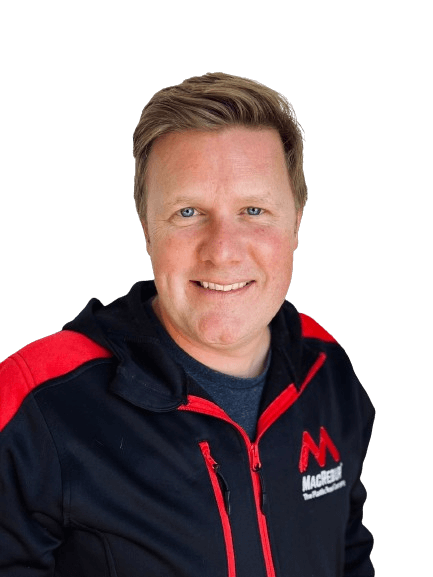
Toby McCartney
Director and Co-Founder
Toby McCartney
Director and Co-Founder
Toby had the original idea of using waste plastics in roads. Toby is responsible for the marketing and PR and has successfully run three rounds of crowd-funding, gaining investment of over £7 million to help grow the company since its incorporation in 2016. Toby set up and now looks after MacRebur Turkey Limited, a new subsidiary of MacRebur's business.
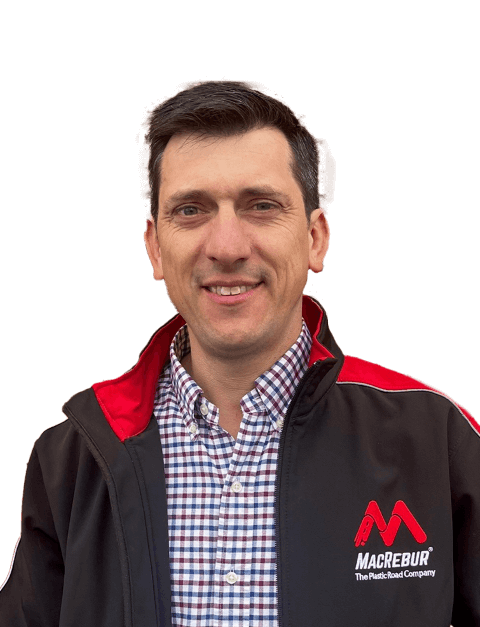
Gordon Reid
Director and Co-Founder
Gordon Reid
Director and Co-Founder
Gordon has been responsible for product development and has built a team who design and build all of MacRebur's recycling machines and addition systems. Gordon also looks after and runs MacRebur's UK contracting business.
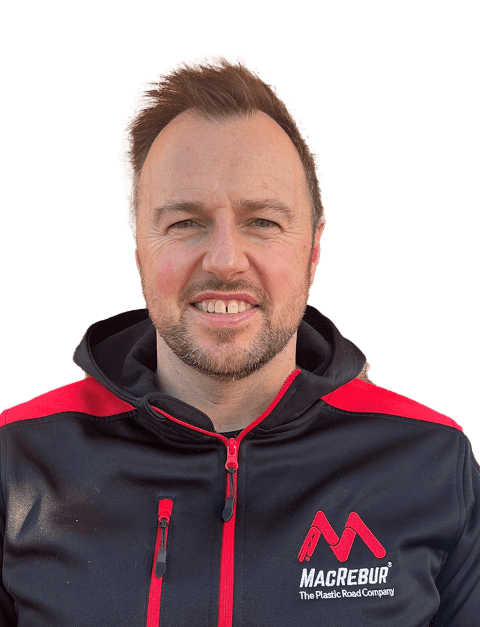
Nick Burnett
Director and Co-Founder
Nick Burnett
Director and Co-Founder
Nick looks after the Lockerbie office members of staff as well as human resources, and is in charge of MacRebur's environmental management and Contracts. Nick also looks after MacRebur's financial accounts together with our in-house accountant, Julie Frood. Nick works together with CMS, MacRebur's chosen lawyers, who manage MacRebur's contracts, patents and IP.
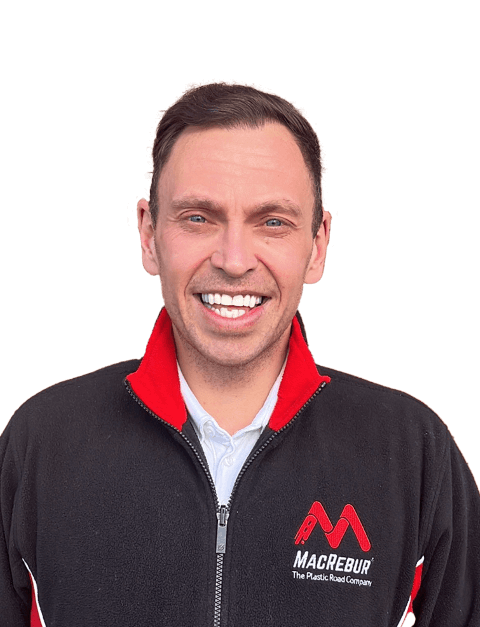
Roddy McEwen
Operations Manager
Roddy McEwen
Operations Manager
Roddy looks after business development in various countries outside of the UK. Roddy facilitates new and existing clients and is responsible for developing business relationships in countries Macrebur is working in across the world.
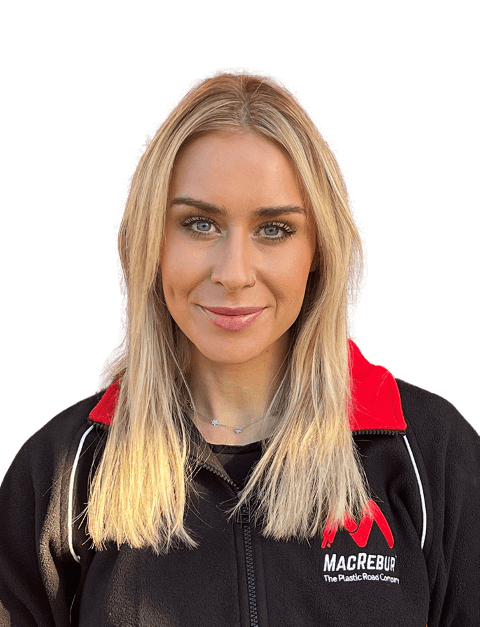
Emily Jackson
International Business Relationship Officer
Emily Jackson
International Business Relationship Officer
Emily looks after MacRebur's worldwide logistics, making sure equipment and products get from a MacRebur site to the customer. Emily is in charge of waste plastic sourcing and research in various countries. As MacRebur's relationship manager, Emily maintains MacRebur's relationships and builds rapport with customers around the world.
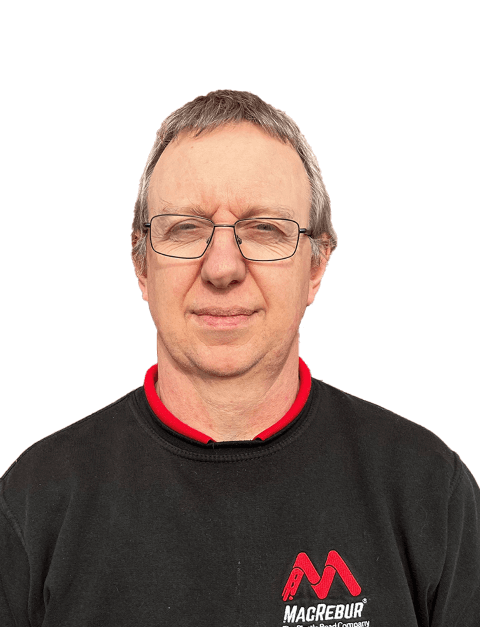
Darren Foster
Asphalt and Bitumen Technical Manager
Darren Foster
Asphalt and Bitumen Technical Manager
There isn't anything Darren doesn't know about asphalt and bitumen due to his past experience of running an asphalt plant and various jobs in the bitumen testing field. Darren spends his days in MacRebur's laboratory and is in charge of all of the asphalt and bitumen testing, as well as the technical specifications of MacRebur's products.
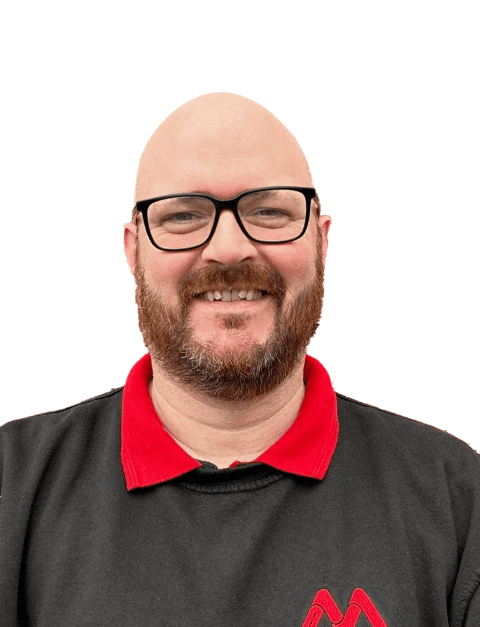
Cammy Lauder
Compliance Officer
Cammy Lauder
Compliance Officer
Cammy is in charge of the quality control management and company Health, Safety and Environmental control for MacRebur's Lockerbie site, as well as MacRebur's ISO certifications, various approvals and product quality control across the world.
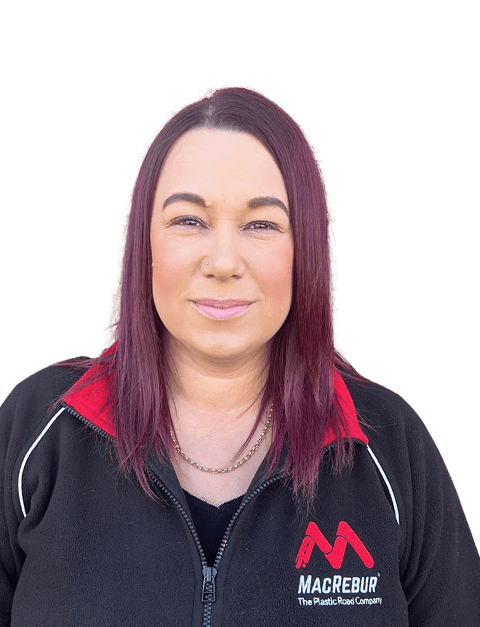
Julie Frood
Accounts Assistant
Julie Frood
Accounts Assistant
Julie works together with Nick to compile Macrebur's financial accounts each month. Julie is the smiler of the team and so sits in the reception office to welcome customers into the MacRebur Lockerbie facility.
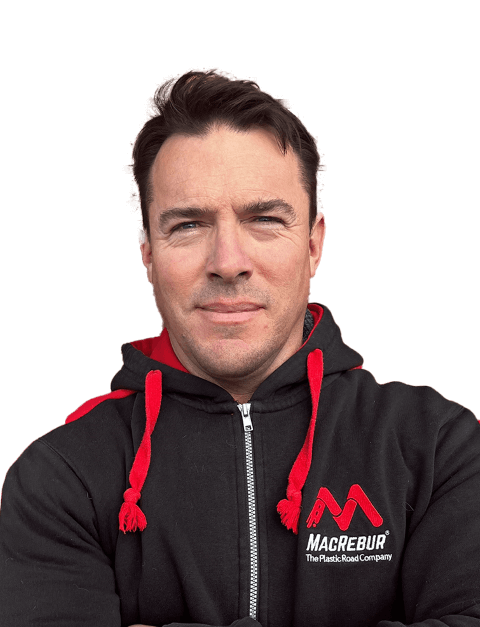
Jeff Jackson
Facility Development Officer
Jeff Jackson
Facility Development Officer
Jeff builds and maintains all of MacRebur's machinery and is in charge of the manufacturing machines and addition systems needed to recycle and supply product in to clients.
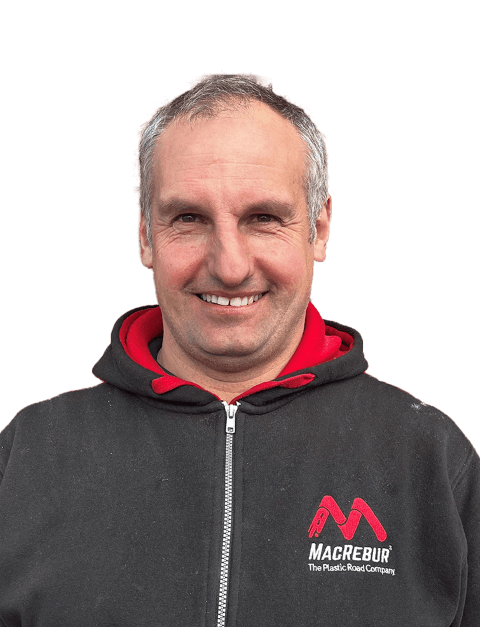
Douglas Lockie
Manufacturing Officer
Douglas Lockie
Manufacturing Officer
Dougie manages MacRebur's warehouse facility and makes the product ready for sale. From granulating to drying and bagging product, Dougie oversees the manufacturing process, from taking raw waste plastics into the yard right through to getting them made ready for sale.
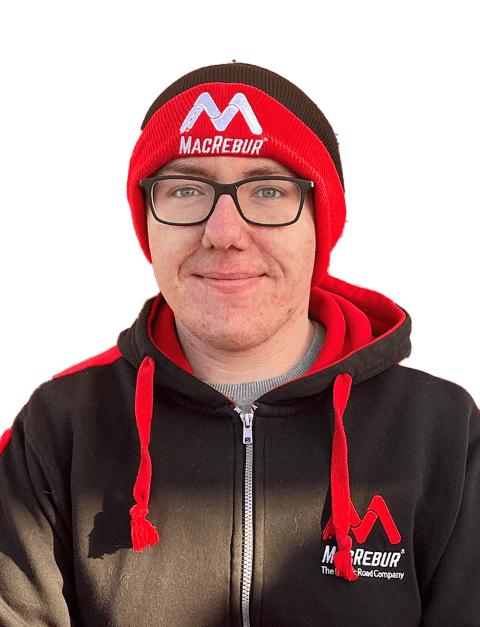
William Gale
Manufacturing Operative
William Gale
Manufacturing Operative
William works under Dougie to help make the MacRebur product ready for sale.
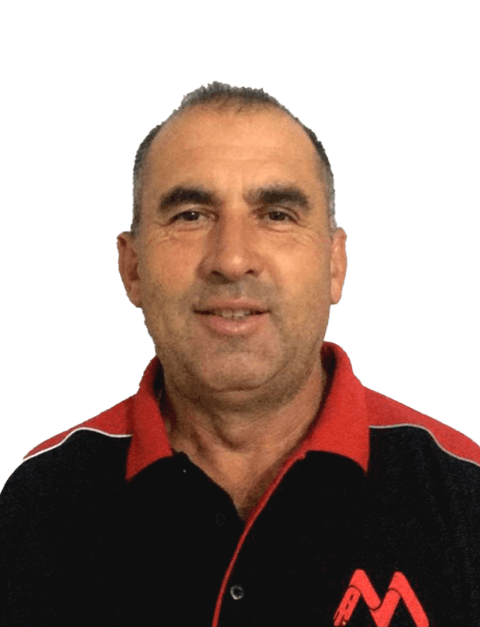
Durmus Yeter
Manufacturing Officer (MacRebur Turkey)
Durmus Yeter
Manufacturing Officer (MacRebur Turkey)
Based in Turkey, Durmus works in a multi-faceted role, managing MacRebur's Turkish warehouse facility and working closely with Toby to ensure the product is ready for sale.